The Significance of Welding WPS: Ensuring High Quality and Safety in Your Jobs
The Significance of Welding WPS: Ensuring High Quality and Safety in Your Jobs
Blog Article
Mastering Welding WPS Requirements: Ideal Practices and Techniques for Top Quality Welds
In the realm of welding, understanding Welding Procedure Spec (WPS) criteria is a vital part that directly influences the top quality and honesty of welds. Sticking to these requirements guarantees uniformity and dependability in welding end results. Nonetheless, attaining excellence in welds surpasses just recognizing the requirements; it entails carrying out best techniques and strategies that elevate the craft to a level of precision and ability that distinguishes the standard from the phenomenal. As we browse through the ins and outs of welding WPS standards, revealing crucial understandings and methods for accomplishing top-tier welds will certainly be vital for welders looking for to succeed in their craft and produce welds that stand the test of time.
Comprehending Welding WPS Criteria

Comprehending WPS standards is vital for assessors, engineers, and welders associated with welding operations. By adhering to WPS standards, welders can create welds that satisfy the needed mechanical homes and structural stability. Inspectors depend on WPS paperwork to verify that welding treatments are being followed appropriately and that the resulting welds are of premium quality. Engineers make use of WPS standards to make welding procedures that make certain the longevity and reliability of bonded structures.
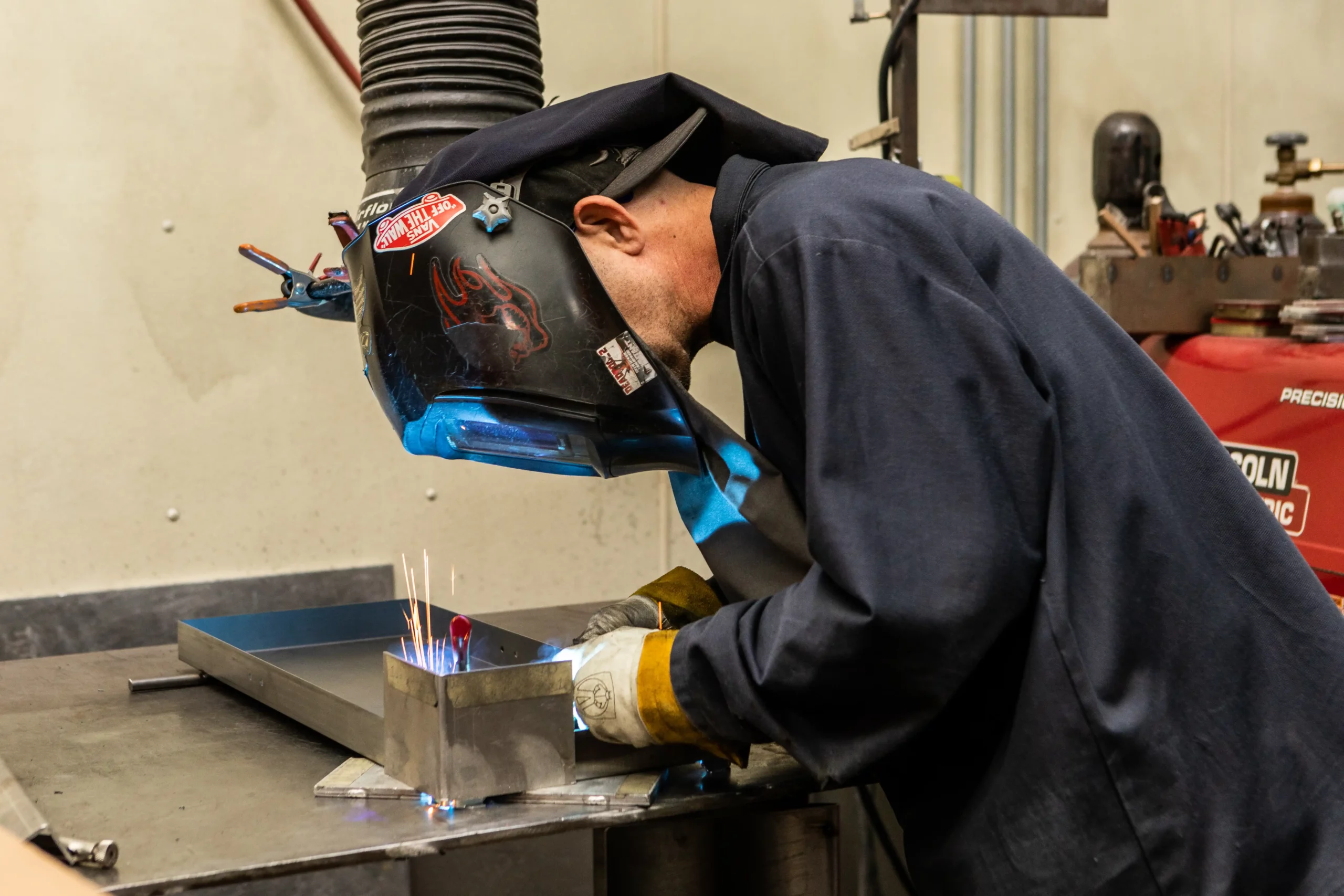

Important Tools for Quality Welds
Mastering welding WPS standards is important for welders to effectively utilize the essential tools needed for generating top quality welds. Among the most essential tools for top quality welds is a welding equipment. The kind of welding maker needed depends on the welding process being made use of, such as MIG, TIG, or stick welding. Welding headgears are likewise important to safeguard the welder's eyes and face from sparks, warmth, and UV radiation. In addition, welding gloves made of durable and heat-resistant products protect the hands from burns and injuries. Clamps and magnets aid hold the work surfaces together safely during the welding process, making sure accurate and precise welds. Wire brushes and damaging hammers are crucial for cleaning up the weld joint before and after welding to get rid of any type of impurities that could affect the top quality of the weld. Finally, a measuring tape and angle mill are helpful devices for guaranteeing proper placement and preparing the workpieces for welding.
Trick Methods for Welding Success
To achieve welding success, one need to understand the essential strategies essential for creating high-quality welds. One important method is keeping the right arc size. Keeping the electrode at the ideal range from the work surface is vital for producing solid, uniform welds. In addition, managing the traveling rate is paramount. Moving as well promptly can result in inadequate infiltration, while relocating also slowly can result in excessive heat input and possible defects. Proper control of the electrode angle is one more crucial strategy. The angle at which the electrode is held can affect the grain form and infiltration of the weld. In addition, making certain constant weapon angle and direction of travel is essential for harmony in the weld bead. Last but not least, maintaining a steady welding and a consistent hand position throughout the process is essential to achieving accuracy and uniformity in the welds. By understanding these vital strategies, welders can raise the high quality of their work and accomplish welding success.
Ensuring Compliance With WPS Specifications
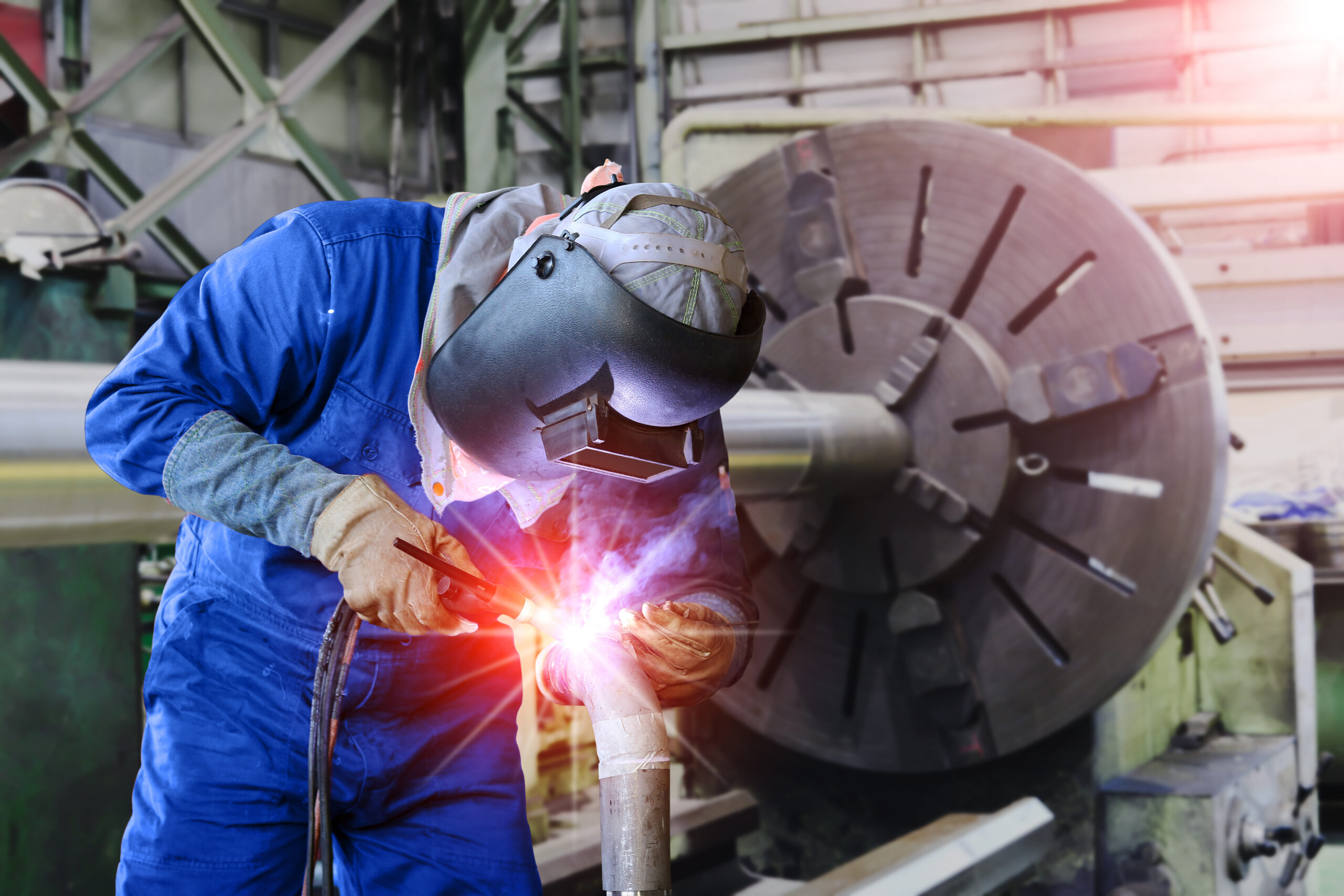
In addition, welders ought to undertake training to familiarize themselves with the WPS criteria pertinent to their job. Routine audits and evaluations need to be conducted to verify that welding activities line up with the recommended WPS guidelines. Additionally, keeping thorough records of welding specifications, tools calibration, and evaluation outcomes is critical for demonstrating conformity with WPS standards - welding WPS. By carefully adhering to WPS requirements, welders can guarantee that their work meets the required top quality levels and adds to the total success of the welding job.
Troubleshooting Common Welding Issues
When encountered with typical welding issues, identifying the source is important for efficient troubleshooting. One widespread trouble is the visibility of porosity in welds, usually triggered by impurities such as corrosion, oil, or over here moisture. To resolve this, ensuring appropriate cleaning of the base metal prior to welding and utilizing the appropriate protecting gas can considerably reduce porosity. An additional problem often experienced is absence of combination, where the weld stops working to correctly bond with the base product. This can come from insufficient warmth input or improper welding method. Adjusting criteria such as voltage, wire feed speed, or travel speed can assist enhance fusion. Furthermore, distortion, cracking, and spatter prevail welding challenges that can be minimized with proper joint prep work, constant warmth control, and picking the ideal welding consumables. By thoroughly recognizing these usual welding problems and their root triggers, welders can efficiently repair problems and accomplish top quality welds.
Final Thought
To conclude, grasping welding WPS standards requires an extensive understanding of the guidelines, using important devices, and implementing essential strategies Clicking Here for successful welds. Get More Information Ensuring conformity with WPS requirements is critical for producing quality welds and staying clear of typical welding problems. By adhering to ideal practices and strategies, welders can accomplish trustworthy and consistent outcomes in their welding jobs.
In the world of welding, mastering Welding Treatment Specification (WPS) requirements is a critical element that directly affects the high quality and honesty of welds.When delving right into the world of welding practices, an essential aspect to comprehend is the importance and details of Welding Treatment Requirements (WPS) criteria. WPS criteria provide a comprehensive standard for welding procedures, ensuring consistency, top quality, and safety and security in the welding procedure. The type of welding machine needed depends on the welding procedure being made use of, such as MIG, TIG, or stick welding.Attaining welding success through the mastery of key techniques demands an extensive understanding and adherence to Welding Treatment Spec (WPS) requirements.
Report this page